At Boeing, the aircraft maker has had its wake-up call since the January 5 event when a door flew out on a Boeing 737 MAX aircraft from an airborne aircraft that belonged to Alaska Airlines. The event, which happened on American soil, brought the focus and scrutiny on Boeing, which is currently subject to multiple investigations regarding the lapses that led to this event. In a rare behind-the-scenes peek, Boeing took journalists to its Renton plant to show how it was fixing its culture and processes after this event, bringing some gaps to the fore. LiveFromALounge joined the briefing.
Missing paperwork caused the Alaska door plug event.
In a briefing led by Elizabeth Lund, Boeing’s senior vice president of Quality for Boeing Commercial Airplanes, the company explained that the fuselage for said aircraft (registered N704AL) arrived at their Renton factory in the summer of 2023 with certain defects from its supplier (Spirit Aerosystems, Wichita). These defects concerned five rivets that did not meet specs. Over the days, it was decided that these rivets needed to be replaced rather than rectified.
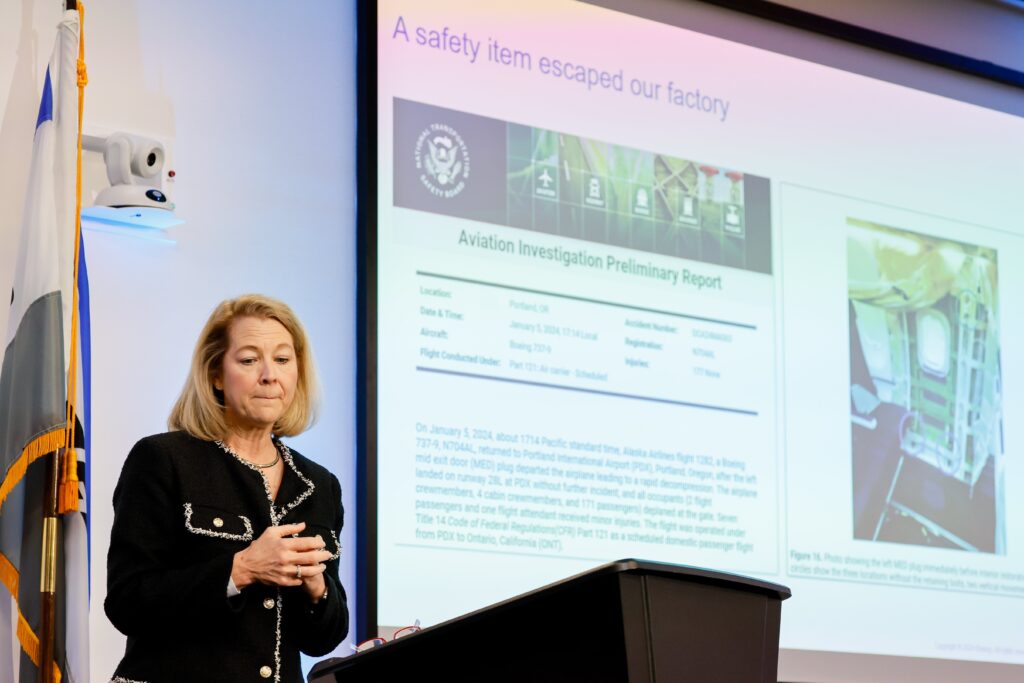
Elizabeth Lund, Senior Vice President, Quality at Boeing, speaks to gathered media in front of a slide detailing the plug door blow-out that occurred on Jan. 5, 2024, on Alaska Airlines flight 1282 at the Boeing 737 factory (Jennifer Buchanan/Pool photo by The Seattle Times)
In their course of business, Boeing team member(s) removed the door panel to replace the rivets but failed to record the removal in the paperwork. However, a different team took over the aircraft and moved it to a different location later in the production process, and they put the door plug back on for the move. The aircraft never had a record of the door plugs being removed, so they never went back on to fix the issue later. Boeing wouldn’t clarify if this miss was on the account of one person or a team, deferring to the ongoing NTSB investigation.
Renton is the only location worldwide where Boeing assembles their 737 aircraft across three assembly lines. Assembling one aircraft usually takes ten days over all three shifts.
Doorplug event sets off quality reorganisation across the factory and organisation
Boeing set about doing a deep dive into its systems and processes, talking to its regulator, customers, employees, and quality auditors, amongst others, to fix its quality issues. The OEM, which has been incrementally building in improvisations on the assembly process that were set out decades ago, took a closer look at all its processes to identify and fix issues. While at it, the aircraft manufacturer also changed things around its working relationship with Spirit Aero, which it hopes to acquire back sometime soon.
The OEM reshuffled its management, bringing in a new set of eyes to take on key roles after the January 5 events. On February 21, 2024, six weeks after the events at Alaska Airlines, Elizabeth Lund was brought in from leading the airplane programmes around Boeing into the position of senior vice president for BCA Quality, where she leads quality control and quality assurance efforts. Also, Katie Ringgold was brought in as vice president and general manager of the 737 programme and the company’s Renton site. Both executives were present during briefings and shop floor walkthroughs for select media at Boeing’s Renton site earlier this week.
Boeing’s people on its frontline, the mechanics and other staff responsible for assembling the aircraft talked about the emotional toll the scrutiny they are being put through is taking on them. “Yeah, it’s tough here sometimes,” Bill Riley, who has been a quality inspector at Boeing for 16 years, said. “We’re human like everyone else obviously … And it’s our work that’s being scrutinised and stuff like that.”
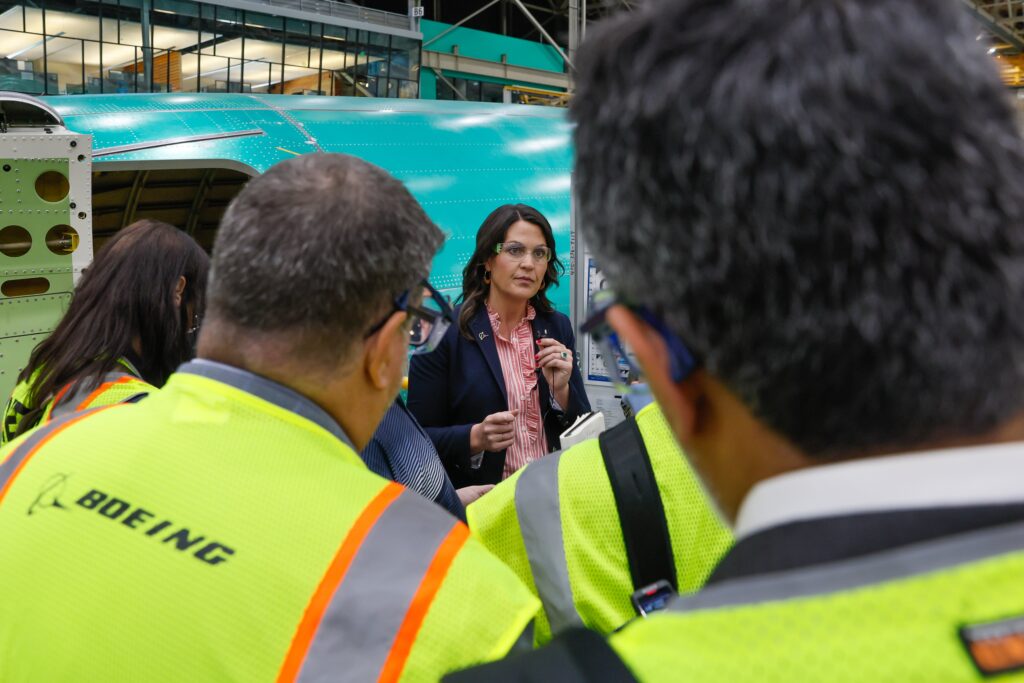
Katie Ringgold, Vice President and General Manager 737 Program and Renton Site Leader, speaks to gathered media at the Boeing 737 factory (Jennifer Buchanan/Pool photo by The Seattle Times)
“That’s how our team feels; they obviously feel bruised right now. And our job is to listen, and our job is to take time to heal and double-down and focus on exactly what Bill just walked you through, and that’s how we’ll get through this. There’s a lot to be proud of, but there’s a lot of work to do,” Katie Ringgold, vice president and general manager of Boeing’s 737 programme, added.
Back to basics: Boeing’s fix to the quality issues
When Boeing analysed its collected feedback, which consisted of over 30,000 inputs, it combined it into ten broad themes. Boeing said it had to hire many more new staff to work on its aircraft assemblies, given it noticed that many of its long-timers exited the company during the MAX grounding, which coincided with the pandemic. The company explained that they were not let go but moved on of their own will. In a sense, it had lost its institutional memory and experience, had been replaced with new staff who did not have the same depth of experience to catch the issues that might exist, and it set out to rectify it.
Many new and senior employees are being retrained, and all new hires now get at least two additional weeks of training at the Boeing Foundational Training Centre (on-site) before they enter the production floor. To bring back some of the experience it lost, Boeing has rehired up to 160 people who’d left Boeing to come back and train the others as coaches on the assembly line, doubling down on its peer mentoring efforts.
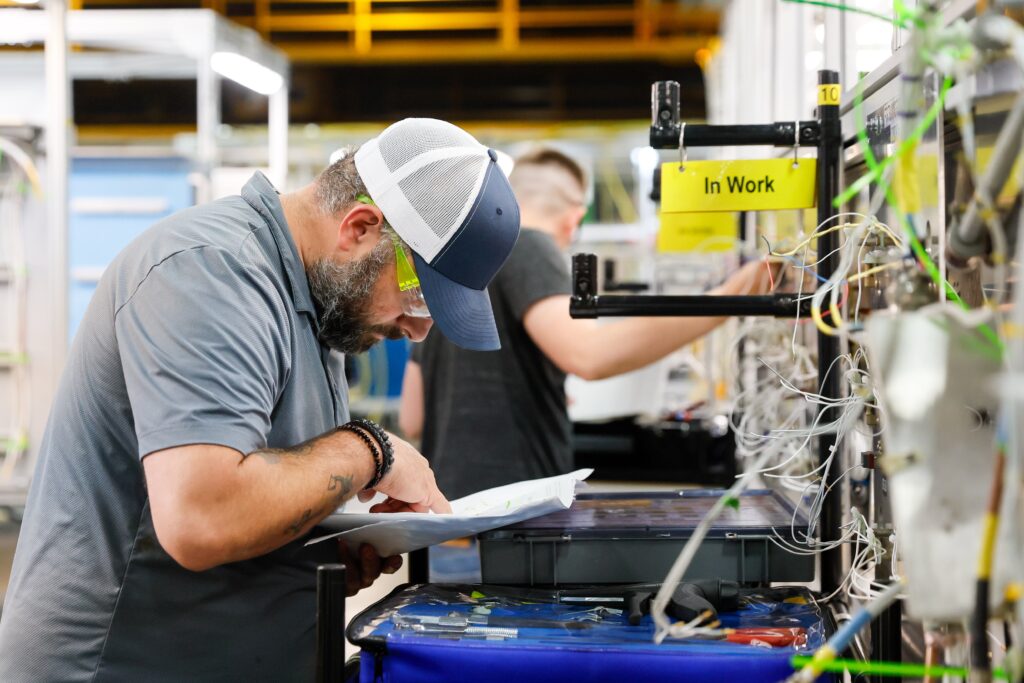
Timothy Jankowski studies a manual as he trains on the electrical systems at the Foundational Training Center Tuesday (Jennifer Buchanan/Pool photo by The Seattle Times)
The company held quality stand-downs across 20 locations, taking the day to stop work, talk about quality and hear the inputs of their employees as to what they could do better. The company now continues to put in an hour every week (across all three shifts) where employees on the floor stand down to discuss concerns and how they can improve. Not just that, more digital efforts have been introduced across the workflow, for instance, to track Work in Process items, which would not have been logged into a system earlier.
Regarding quality efforts, Boeing employees across the workflow have the power to hold up the production line if they believe something is not right and needs to be fixed. There is also a huge focus on reducing instances of “travelled work”, where a job is not completed on its station but rather passed further down the workflow to be taken care of “later”. An out-of-sequence event can increase the risk of mistakes. Making it more stringent to allow the aircraft to move down the production line has allowed Boeing to cut the amount of travelled work by about 50%.
For instance, during the assembly line tour, a Boeing representative pointed at the empty day-five slot on one of the three assembly lines. Employees had identified an issue with the fuselage. Erstwhile Boeing would have moved the aircraft along the line and addressed the issues later, but now, aircraft cannot move forward till they comply with a quality check at every station to ensure that there are no major steps left that they might need to revisit later.
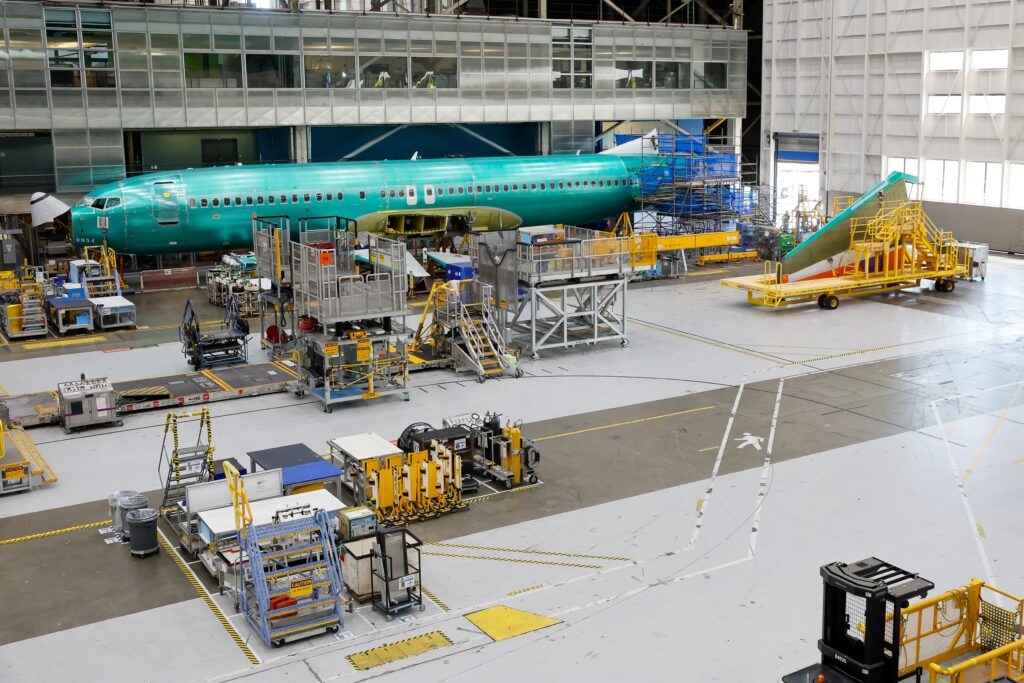
An open space on the floor marks a noticeably absent aircraft in flow day 5 at the Boeing 737 factory (Jennifer Buchanan/Pool photo by The Seattle Times)
Boeing representatives also mentioned that they have increased their scrutiny of the fuselages shipped to them from Wichita. By positioning their inspectors there, they see a large reduction in the quality issues that now travel to Renton instead of being fixed at Wichita itself. Earlier, issues were identified at Renton, which sometimes required back and forth with Spirit Aerosystems staff positioned at Boeing in Renton to fix those issues. The supplier inspections have allowed Boeing to make the MAX more quickly once the fuselage arrives at its Renton facility. “The benefits have been really tremendous,” said Ms. Lund.
Boeing mentioned that production manuals are being simplified so that instructions are easier to understand for those who speak English as a second language. Boeing has also slowed production, but, hopefully, it will soon be near its pre-crisis pace. The FAA, Boeing’s regulator, has currently capped Boeing’s production at 38 737 MAX planes per month.
“My focus is not on rate. My focus is on stabilising this factory,” Katie Ringgold said.
Bottomline
At Boeing’s Renton factory, there has been a switch in the approach towards quality, with many parts of the production process going back to basics, and at a slow rate to try and capture the defects and resolve them before they get out of the door of Boeing’s plants and into the open. The OEM has worked for months to tweak its processes and make it better than the prior approach.
What do you think of Boeing’s approach to quality control across its 737 production process?
Liked our articles and our efforts? Please pay an amount you are comfortable with; an amount you believe is the fair price for the content you have consumed. Please enter an amount in the box below and click on the button to pay; you can use Netbanking, Debit/Credit Cards, UPI, QR codes, or any Wallet to pay. Every contribution helps cover the cost of the content generated for your benefit.
(Important: to receive confirmation and details of your transaction, please enter a valid email address in the pop-up form that will appear after you click the ‘Pay Now’ button. For international transactions, use Paypal to process the transaction.)
We are not putting our articles behind any paywall where you are asked to pay before you read an article. We are asking you to pay after you have read the article if you are satisfied with the quality and our efforts.
Leave a Reply